 |
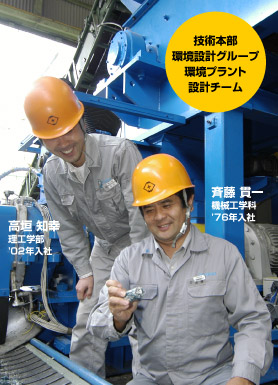 |
富士車輌の事業の大きな柱となる環境装置・プラントの分野で同社ならではの新発想の製品が生み出されました。それがフジRPF(REFUSE
PLASTIC&PAPER FUEL)ステーションです。廃プラスチックを破砕・成形して燃料化するこのプラント、業界初となる小型化や省コストを実現した斬新なモデルでした。開発を担当した齋藤貫一さんと高垣知幸さんに製品化までのプロセスをうかがいました。
「もともと大規模なプラントだったRPF製造設備を小型化したいという要望がありました。そこで考えたのが破砕・成形という2つのプロセスを1台の機械でおこなうというものでした。また自動化することで各工程のオペレーターも削減できるという省スペース省コストのRPFでした。しかし比較的簡単に考えていた設計でしたが問題は山積みでした」(齋藤)。
|
「まず最初にぶつかったのが破砕と成型の処理スピードの違いです。破砕に比べて成形は時間が掛かります。従来は破砕したプラスチックをいったん貯めておいて別工程として成形していたんですが、今回はそれを同じラインで処理しようとしたので問題が起きました。“うまくいかないかも……”と弱気になったこともありました。しかし試行錯誤の末、電気制御を加えることで成形の処理に合わせて破砕の工程をコントロールすることに成功したんです。各工程がスムーズに流れるようになったときにはホッとしましたよ」(齋藤)
「いえ、新たな問題が発熱量でした。プラスチックが発する熱でどろどろに溶けてしまうなど処理が安定しなかったんです」(齋藤)
「対策としてヒーターや温度を下げる水の噴霧などを追加しました。しかし処理の不安定さは収まりませんでした。プラスチックに関しての知識はほぼゼロだった私は資料を調べたり知人の技術者に意見を聞いて解決策を探りました。そんな中で関連会社の技術部長だった人から重要なアドバイスをもらったんです。それは“プラスチックは素材によって溶ける温度がかなりバラツキがあり混ぜて処理するのは難しい”ということでした。そこで処理するプラスチックの比率をあらかじめ決め、設定温度を前後5℃の範囲で安定させる温度管理のシステムを作り上げたんです。今では投入する素材を見ただけでだいたいの設定温度はわかるようになりました」(高垣)
その後、成形工程の温度調整に必要な水の噴霧も自動化に成功。ついに目標としていた省コスト省スペースの製造設備が完成しました。難しいオーダーをやり遂げたお二人にとって設計の醍醐味とはどのようなものでしょう?「自分たちでプランした新商品が利益を生み出すことが最大の醍醐味です。展示会などでデモ機をテストしていると客の評価が聞けます。そのときに“売れそう”という実感がヒシヒシと伝わってくるんです」(齋藤)
「初めての試運転、そこで狙い通りに動作して客先の担当者が頷く瞬間ですね。満足してもらえているという感じが伝わるこの時、自分の作ったものに誇りを感じます」(高垣)
「とにかく技術者は好奇心旺盛であることです。何にでも興味を持って取り組んで下さい。それと私が入社当時教えられたのは“とにかく考えろ”でした。“どのぐらい考えるんですか?”と質問したら“吐き気がするぐらい考えるんや!”と指導されたのが今も心に残ってます。ただしリフレッシュも大切。私の場合、休日は設計のことを忘れて釣りや畑作りでリフレッシュしてます」(齋藤)
「日々の仕事に追われて新しい知識吸収の勉強をおろそかにしがちですが、必ず一定の時間を知識吸収のために残しておくべきです。意外にそこから新しい設計のヒントが生まれたりするものです。そして自分を信じて妥協のない設計をすることです」(高垣) |
|
|
 |